Gas-tight Ozone System
V500-V1000
500ml Gas-tight Infusion Vessel with Multi functional features for ozonating solutions. Glassware is made is made in the United kingdom and is Duran 3.3 Laboratory Grade Glass.
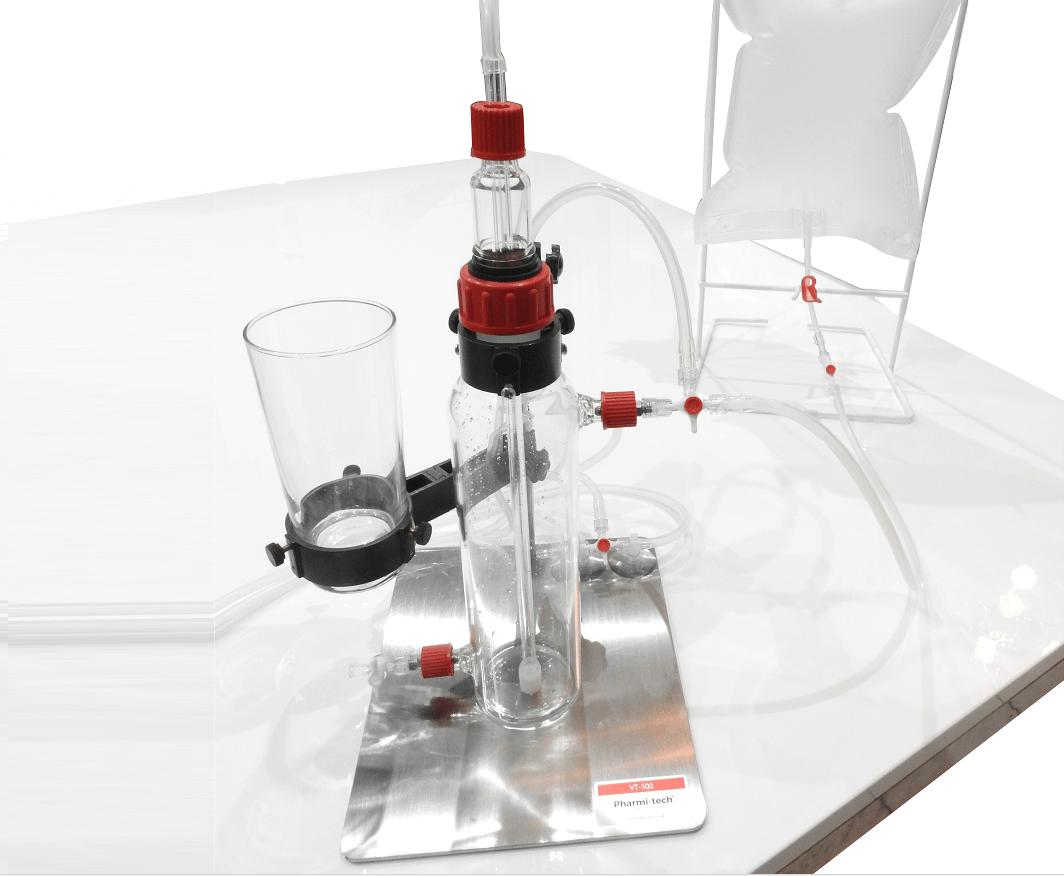
Introduction:
There are many varieties of glassware specific to ozone applications, all of which come in different shapes, size and functionalities. The
glassware material quality is a primary factor to consider before purchasing any glassware adapted for the use of ozone applications. Borosilicate glass is commonly used for performing Medical applications and Laboratory experiments for its low coefficient of thermal expansion and superior chemical resistance. The qualities of Borosilicate Glass are associated to its ability in abrasive environments to not degrade and remain structurally and chemically stable.
Generally speaking there are 3 types of glass in the commercial markets, Borosilicate, soda-lime silicate and phosphates. Glass compositions are engineered to exhibit different physical, chemical, and optical properties, such as removal of Boric Oxide content (low Alkali) in borosilicate glass. Different applications demand specific types of glass and manufacturing processes. The three common glass compositions are highlighted below.
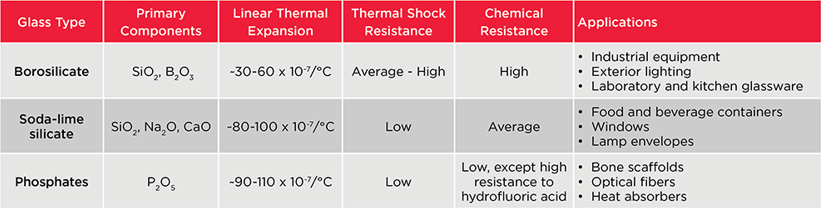
Convenient features, Functionality and Efficiency
The key features to ozone glassware have all been adapted in one way or another to suit the environment and application. During our research we found a lack of functionality and convenient features among companies, we found minimum capabilities of performing more than a single function specific to an application. Diverse functionality not only increases application diversity, it creates a broader spectrum of use with a single unit. Our aim was to design a single piece of glassware capable of performing multiple applications.
Ozonated Solutions
There are many machines that produce ozonised water in clinical environments using a variety of gas feeding systems. First Method involves ozone entering though a glass stem inlet (downwards pressure feed), and the second method, ozone entering the base of a vessel (rising feed) allowing for maximum saturation. Shape and size of vessels or machines that produce ozonised water having a rise/feed of ozone gas offers effective surface area saturation qualities. Surface area issues arise though glass stem inlets due to ozone being infused in a centered column of gas. We found more effective results by changing the shape of the glassware into a tube or cylinder, the cylinder shape was an attempt to equalize the consistency and maximize the surface area.
Functionality
Elements of the ozonation procedure and functionalities will depend on the type of application required. Glassware functionality was a main priority, along with a system design that remained gas tight throughout applications. The glassware has two twin ports that allow
pressurized and vacuum options, these ports can be converted into manual manifolds allowing control over pressure and water flow for gas tight transfers.
Basic functions
- Syringe automatic filling
- Humidifying
- Pressurizing (Gas Tight)
- Siphon Function
- Height adjustment inlet stem
- Vacuum function
- Multiple attachments luer lock
Material Choice & Quality
The purpose of creating an all-in-one unit (closed system) for a variety of applications came with various challenges relating to material quality and interchangeable parts. We designed the twin ports to harness removable connectors made from stainless steel 316 or Polycarbonate that are tightly held in place by special PTFE compression seals. The plastics that come installed with the glassware are 100% ozone resistant and are fully removable for replacement and material reconfiguration.
Instructional use:
The vessel is to remain gas tight in all applications where possible, the glassware was designed to limit ozone gas from escaping and therefore should remain a separate unit when producing liquids for inhalation or topical purposes. When producing ozonated water it is advised to use the siphon port on the lower left side of the vessel, this allows control over the flow of ozonated water into a separate flask for inhalation or attachable syringe for gas-tight solution transfers.
The tubing attachment material quality should preferably be platinum cured silicon tubing. The vessel is supplied with the correct tubing and connectors for applications.
It is not advisable to pressurize the vessel for more than a 10 second period if your generators are not installed with APRV (automatic Pressure release valve) this could result in damage to your generator, inconsistent ozone concentrations and cause internal tubes to burst.
Cleaning method: Ultrasonic cleaning uses ultrasound to remove contaminates in distilled water and is an effective way to clean glassware used for ozone.